By being a part of Callaghan Innovation's Digital Lean pilot programme, Oasis Engineering are more productive and poised to entre new lucrative markets.
At a glance
- Already adopting Lean methodologies, Oasis Engineering wanted to continue to streamline manufacturing processes in a bid to combat a highly competitive industry and price pressures.
- Oasis joined Callaghan Innovation’s Digital Lean pilot programme, enabling integration of new digital technologies and adoption of more of a data-driven approach to production.
- Through Digital Lean and Industry 4.0 integration, Oasis has been able to deploy staff to higher-value tasks, employ more dedicated engineers, and are set up to enter the fast-growing hydrogen fuel systems market.
Industry 4.0 will be central to that [product expansion]. Without Callaghan Innovation, we wouldn’t have had the knowledge or resources to start down that path.
- Kevin Flint - General Manager, Oasis Engineering
A love of Lean leading the way
A competitive industry with strong price pressures. But Tauranga-based Oasis Engineering is up for the challenge, producing precision-machined, stainless steel products for global customers in the energy and transport sectors.
To make sure it could stay ahead of larger competitors however, Oasis Engineering adopted Lean methodologies. Paying dividends, the approach was behind a dramatic improvement in business performance when it came to shipping products to customers, with shipping times met 98.5 per cent of the time compared to 65 per cent originally.
“Lean is now ingrained in our day-to-day work routines and we even use the strategies at home. It’s an effective and simple way to work and live more efficiently. It's just about improving the process and repeating,” Oasis Engineering general manager Kevin Flint says.
From Lean to Digital Lean, thanks to Callaghan Innovation
After a visit to ELAFLEX - a German refuelling equipment specialist who bought a stake in Oasis in 2017 - Flint witnessed ‘Industry 4.0’ for the first time. The next step in the digitisation of manufacturing was here.
“I hadn’t heard about Industry 4.0 previously, but the more I looked into it, I saw that it was an extension of the Lean approach we had been following,” says Flint.
As a result, it was a no-brainer for Oasis to join other Kiwi manufacturers, including New Zealand Steel, Lion and Methven, in Callaghan Innovation’s Digital Lean six-month pilot programme in 2020. It was the on-the-ground support and funding they needed to put some of those new technologies and approaches to work, with Digital Lean’s goal to allow businesses to make small changes in order to really reap the benefits of Industry 4.0.
One area of digital integration thanks to Digital Lean saw Oasis add sensors to equipment to communicate with the operator when a problem was detected. This included the engineers receiving texts when a machine has a problem and stops, and looking at setting up cameras the engineers can look at on their phones to check the machine’s status.
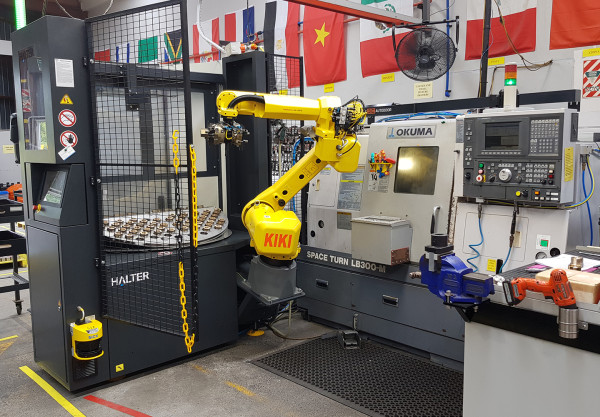
Robot arm with manufactured brass swivels for use on petrol tankers
Digital Lean has also led to a more data-driven approach to Oasis Engineering’s production process. Every engineer and technician on the assembly floor now has a tablet, which they use to record notes and take photos and videos of their work.
“There's a lot of knowledge an individual has in setting up this machinery,” says Flint. “Now we can transfer that knowledge to everyone more easily.”
And lastly, Oasis has also ramped up its use of robotics to load and remove components from factory machines that process the metal components.
Working towards new markets
Integrating Digital Lean is enabling Oasis to innovate for the future, with the improvements helping the business as it looks to expand its product range. With a significant increase in dedicated product development engineers, they’re looking to service the hydrogen fuel market especially, a fuel being pursued as a low-emissions alternative to petrol, diesel or gas.
“ELAFLEX sees us applying our CNG [Compressed Natural Gas] knowledge to the hydrogen market. It’s a huge opportunity,” says Flint.
“Industry 4.0 will be central to that. Without Callaghan Innovation, we wouldn’t have had the knowledge or resources to start down that path.”
As well, Oasis Engineering are now able to deploy staff to higher-value tasks within the business. For example, increased robotics means fewer people are needed for the monotonous production line tasks, with one shop floor worker learning to use computer-aided manufacturing software and spending half their time now in the office refining machining processes.